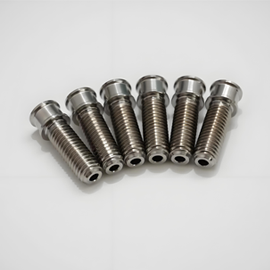
Titanium Alloys Machining Guide: Techniques, Methods, and Applications
A comprehensive overview of the latest techniques and best practices for machining titanium alloys. Learn about their applications, advantages, and challenges to optimize their use in industrial production.
Quote Now!
Titanium Alloys Machining Guide: Techniques, Methods, and Applications
Release time:2024-05-31 | Visits:4671. Introduction
Titanium alloys are renowned for their exceptional strength-to-weight ratio, corrosion resistance, and biocompatibility, making them invaluable in aerospace, medical devices, and automotive industries. However, machining titanium alloys is challenging, requiring specialized processes and techniques. This article delves into the methods, technical considerations, and applications of titanium alloy machining.
2. Basic Properties of Titanium Alloys
Titanium alloys possess several key properties that make them highly sought after in engineering and manufacturing:
High Strength-to-Weight Ratio: Comparable to steel in strength but significantly lighter.
Corrosion Resistance: Excellent performance in seawater and acidic environments.
Biocompatibility: Suitable for medical implants.
3. Classification of Titanium Alloys
Titanium alloys are primarily categorized into three types:
Alpha (α) Alloys: High-temperature performance, commonly used in aerospace.
Beta (β) Alloys: Easier to process, suitable for complex-shaped parts.
Alpha+Beta (α+β) Alloys: Combine the advantages of both, widely used in industrial manufacturing.
4. Titanium Alloys Machining Techniques
Several machining methods are employed for titanium alloys, including:
Cutting: Utilizes high-hardness tools and low cutting speeds to avoid material deformation and overheating.
Laser Machining: High precision, ideal for manufacturing complex parts.
Electrical Discharge Machining (EDM): Suitable for hard-to-machine materials.
4.1 Cutting
Key considerations for cutting titanium alloys include:
Selecting Appropriate Tool Materials: Such as carbide or ceramic tools.
Controlling Cutting Speed and Feed Rate: Low cutting speeds and moderate feed rates help extend tool life.
Using Coolants: Effective cooling and lubrication to reduce cutting heat.
4.2 Laser Machining
Laser machining uses high-energy laser beams for cutting and engraving materials, offering the following benefits:
High Precision: Suitable for producing complex and precise parts.
Non-contact Processing: Reduces mechanical stress and deformation.
4.3 Electrical Discharge Machining (EDM)
EDM removes material using electrical discharges, especially suitable for high-hardness titanium alloys:
High Precision: Ideal for machining intricate and complex structures.
No Need for High Hardness Tools: Material is removed through electrical discharges.
5. Applications of Titanium Alloys Machining
Due to their superior properties, titanium alloys are widely used in various fields, including but not limited to:
Aerospace: Aircraft structural components, engine parts.
Medical Devices: Artificial joints, dental implants.
Automotive Industry: Engine components, exhaust systems.
6. Challenges and Solutions in Machining Titanium Alloys
Common challenges in machining titanium alloys include:
Rapid Tool Wear: Select appropriate tool materials and optimize machining parameters.
Material Deformation and Overheating: Use suitable cooling techniques and control machining speed.
High Costs: Reduce costs by optimizing machining processes and improving material utilization.
While machining titanium alloys presents challenges, using the right techniques and methods can achieve efficient and high-quality manufacturing. Understanding and mastering the properties, classifications, and machining techniques of titanium alloys will help maximize their advantages in industrial production.