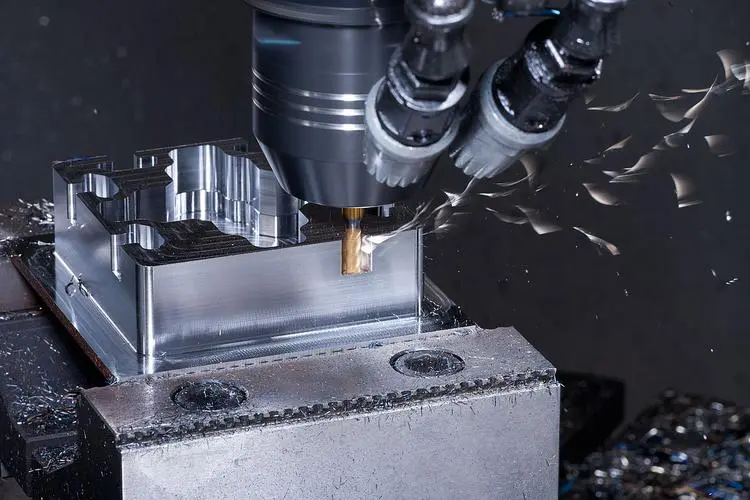
How Does CNC Machining Work: A Comprehensive Guide
Discover how CNC machining works to create high-precision parts through computer-controlled processes. This article provides a detailed overview of the principles, steps, benefits, and wide-ranging applications of CNC machining, showcasing the power of this modern manufacturing technology.
Quote Now!
CNC machining, or Computer Numerical Control machining, is a revolutionary manufacturing process that uses computerized controls to operate and manipulate machine tools. This technology is essential for producing complex parts with high precision and efficiency. In this article, we will explore how CNC machining works, its benefits, and its applications across various industries.
What is CNC Machining?
CNC machining involves the use of computers to control machine tools such as lathes, mills, routers, and grinders. The process starts with a digital 3D design, created using CAD (Computer-Aided Design) software. This design is then converted into a series of commands using CAM (Computer-Aided Manufacturing) software, which the CNC machine follows to shape the material.
The CNC Machining Process
Design and Programming:
CAD Model Creation: The process begins with creating a detailed 3D model of the part using CAD software. This model includes all the specifications and dimensions required for the final product.
CAM Programming: The CAD model is then imported into CAM software, where it is translated into G-code. G-code is the programming language that CNC machines understand, containing instructions for movement, speed, and tooling.
Setup:
Material Selection: The appropriate material, such as metal, plastic, or wood, is chosen based on the part’s requirements.
Machine Setup: The raw material is secured on the CNC machine's worktable. The tools required for the machining process are also installed and calibrated.
Machining:
Execution of G-code: The CNC machine reads the G-code and executes the instructions. This involves precise movements of the machine tools to cut, mill, drill, or grind the material into the desired shape.
Monitoring: During the machining process, operators monitor the machine to ensure accuracy and make any necessary adjustments.
Finishing:
Deburring and Polishing: After machining, the part may require additional finishing processes such as deburring to remove sharp edges and polishing to achieve a smooth surface.
Inspection: The final part is inspected for quality and accuracy, ensuring it meets the design specifications.
Benefits of CNC Machining
Precision: CNC machines can produce parts with extremely tight tolerances, ensuring high accuracy and consistency.
Efficiency: Once programmed, CNC machines can operate continuously with minimal supervision, significantly reducing production time.
Flexibility: CNC machining is versatile and can be used to create complex geometries and intricate details that would be difficult or impossible with manual machining.
Cost-Effectiveness: Despite the initial investment, CNC machining reduces labor costs and waste, leading to cost savings in the long run.
Applications of CNC Machining
CNC machining is used across a wide range of industries due to its versatility and precision. Some common applications include:
Aerospace: Manufacturing of engine components, turbine blades, and structural parts.
Automotive: Production of engine parts, transmission components, and custom car parts.
Medical: Creation of surgical instruments, prosthetics, and dental implants.
Electronics: Fabrication of enclosures, connectors, and heat sinks.
Industrial Equipment: Making parts for machinery, pumps, and valves.
Conclusion
CNC machining is a cornerstone of modern manufacturing, offering unmatched precision, efficiency, and flexibility. Whether you're producing a prototype or mass-producing a product, CNC machining provides the tools and capabilities to bring your designs to life with the highest level of accuracy. By understanding how CNC machining works, you can better appreciate its role in advancing technology and industry.