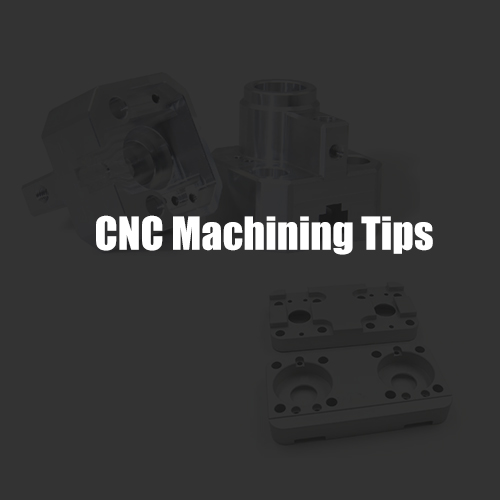
CNC Machining Tips: Optimize Your Design for Precision, Efficiency, and Cost-Effectiveness
CNC machining is renowned for its ability to manufacture customized parts with excellent strength and tight tolerances, making it ideal for mass production. It is currently the most efficient method for creating metal prototypes. Due to its numerous advantages, CNC machining is widely used in many f
Quote Now!
CNC Machining Tips: Optimize Your Design for Precision, Efficiency, and Cost-Effectiveness
Release time:2024-06-05 | Visits:238CNC machining is renowned for its ability to manufacture customized parts with excellent strength and tight tolerances, making it ideal for mass production. It is currently the most efficient method for creating metal prototypes. Due to its numerous advantages, CNC machining is widely used in many fields. Understanding how a CNC machine works is crucial before designing CNC machined parts.
How CNC Machining Works
CNC machining involves removing material from a solid block using high-speed rotating cutting tools to create the desired part according to the drawing. The cutting tool is critical in CNC machining, as it directly contacts the part and removes excess material to achieve the final shape.
Common CNC Cutting Tools
The most common CNC cutting tools, such as the end mill tool and drill, have a cylindrical shank with a specific cutting tip shape and a restricted cutting length. These tools have limitations due to their geometry. For example, internal vertical rectangular corners are difficult to achieve, and deep small holes and undercuts are challenging due to limited cutting lengths.
Tips for Effective CNC Design
To fully leverage the benefits of CNC machining, consider the following design tips:
Adding a Radius in the Internal Vertical Corner
CNC milling tools are cylindrical, creating a radius in vertical corners. A smaller diameter tool reduces this radius, but it can't create a perfectly sharp interior corner. Small tools can work at lower speeds to achieve a small radius, increasing time and cost. Thus, it's advisable to add a radius of one-third the depth of the cavity and use similar radii for internal edges.
Limiting the Depth of Cavities
Tools perform well when cutting cavities up to 2-3 times their diameter. Milling cavities deeper than 4 times the tool diameter increases difficulty and risk of breakage, leading to higher costs. Design pockets with depths less than four times the tool diameter when possible.
Increasing the Thickness of Thin Walls
Machining thin walls is challenging due to deformation or fracture. Thin walls require multiple passes at low depths, increasing vibration and difficulty. Design metal walls with a minimum thickness of 0.8 millimeters and plastic walls with more than 1.5 millimeters thickness to ensure accuracy and reduce machining time.
Limiting the Length of Threads
Longer threads don’t necessarily strengthen connections beyond a certain length. Threads longer than 1.5 times the hole diameter don't add strength. Design threads with a length between 1.5 to 3 times the hole diameter for optimal fastening.
Specifying Necessary Tolerances Only
Higher accuracy increases machining time and cost. Only specify tight tolerances when essential. If a specific tolerance isn't needed, parts will be machined with a standard tolerance of ±0.125 millimeters, sufficient for many non-critical features.
Reducing Small Features
Avoid micro-holes smaller than 2.5 millimeters in diameter unless essential, as they increase machining difficulty and time.
Choosing Engraved Text Over Embossed Text
Engraved text requires removing less material than embossed text. Use Sans-Serif fonts like Arial or Verdana with a minimum size of 20 points. Many CNC machines have pre-programmed routines for these fonts.
Minimizing Setups
Design parts to be machined in as few setups as possible, ideally in one. For instance, a part with blind holes on both sides requires two setups, reducing accuracy and increasing re-aligning time. Fewer setups lead to more precise parts and lower machining times.
By adhering to these tips, you can optimize your designs for CNC machining, ensuring efficient production, cost savings, and high-quality parts. Contact us to discuss your project requirements and experience the precision and reliability of our CNC machining services.