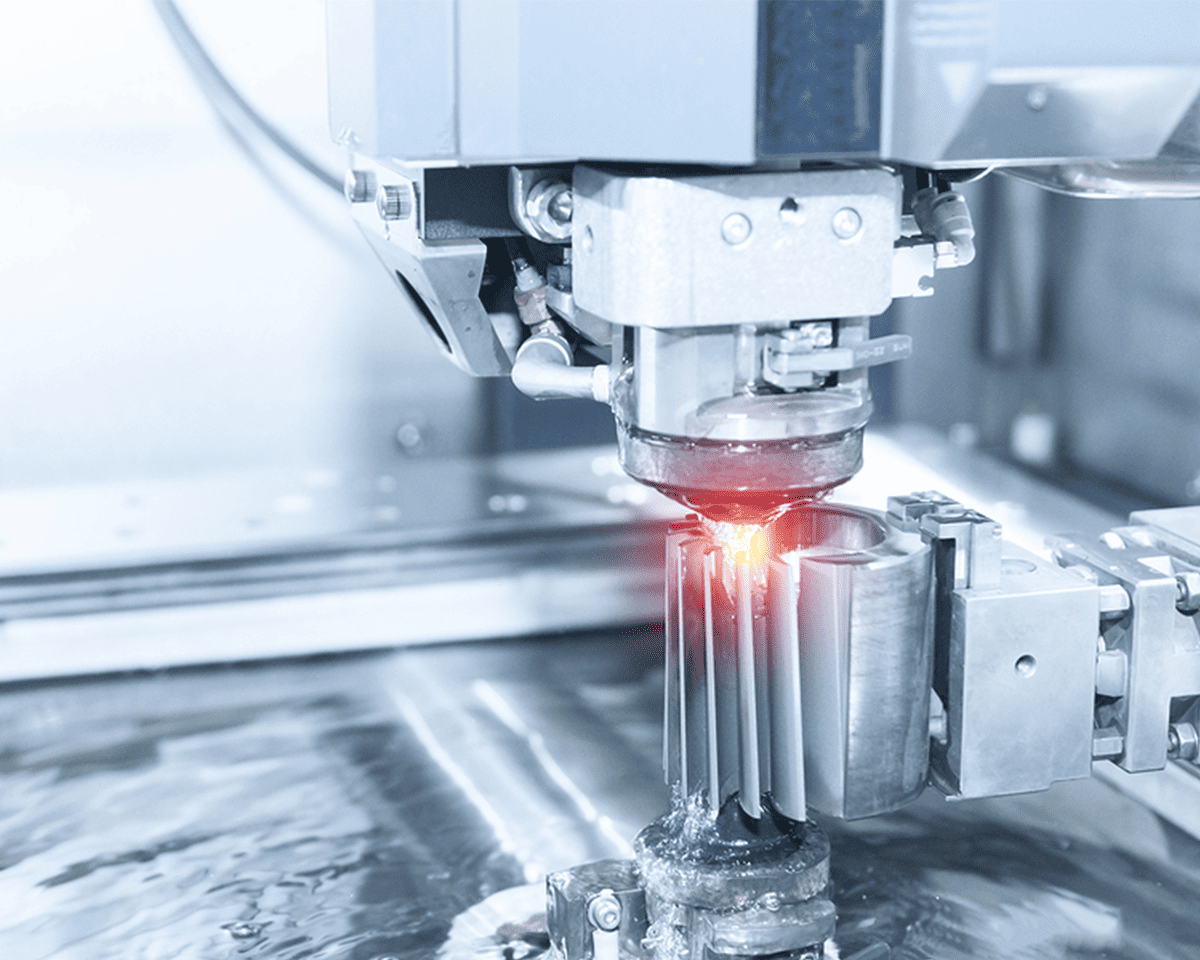
Wire EDM Service
Increase Manufacture or machine the metal parts you want with advanced wire EDM machines. You transfer the CAD data of the product and we complete the production.
GET A QUOTEElectrical discharge machining (EDM) is a manufacturing process that uses electrical sparks to form metal shapes. Because of these sparks, EDM is also known as spark machining. In this process, the desired shape is cut from the metal when a current discharge or spark occurs between the two electrodes. Where the spark occurs, the metal is cut to form the desired shape and separated from the sheet metal.
Increase as one of the most professional CNC machining parts manufacturer, we are equipped with the most advanced wire EDM machines to support our customers. Besides that, services like CNC machining, rapid prototyping, metal casting services, and some others are also available to choose from.
Our Capabilities of Wire EDM
-
We are able to give you a wire EDM manufacturing service by using 4 axis EDM cutting.
-
Our wire EDM tolerances are accurate enough, and they can be controlled within +/- .0001.
-
Various wire diameters are feasible here at JTR, such as 0.006’’, 0.008’’,0.10’’, and 0.012’’.
-
The most advanced machinery and tooling are the basics, which allows us to provide the most precise products.
-
Several CAM software helps us accelerate the adaptability of importing drawings, files, or parts.
Comprehend the Wire EDM Process
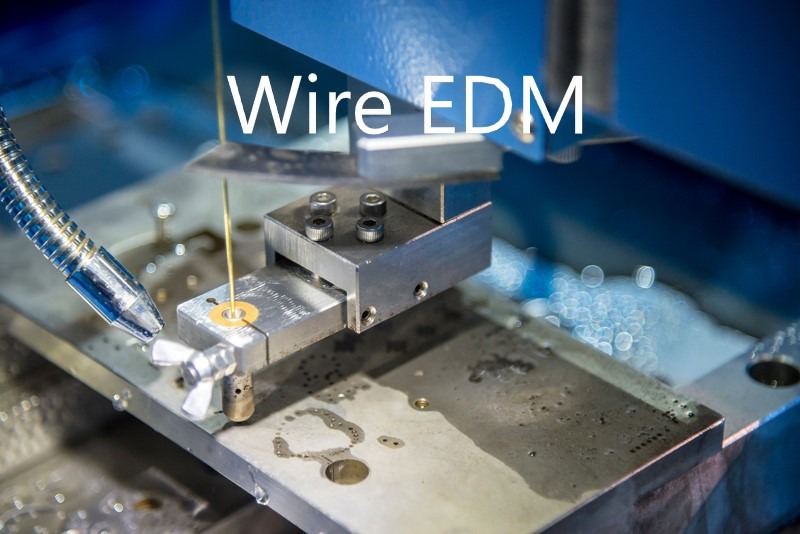
During the wire EDM process, a metal part is put into dielectric fluid, and a wire The wire is passed through the submerged metal part. Electricity is sent through the part to create a spark that ultimately helps create the desired part shape.
When the distance between the electrodes is narrowed, the electric field strength increases, thereby increasing the strength of the dielectric fluid. Under these conditions, current passes more easily between the two electrodes, and each spark causes the element to separate from the metal sheet.
After the current is passed through and the desired shape is achieved, manufacturers sometimes take a process called “flushing,” using a dielectric liquid to help remove any undemanding material or waste from the finished product.
Materials for EDM
Materials options at JTR include various hard-to-handle conductive metals and alloys, which include:
- Tool steels
-
Steel 1018, steel 4130, steel 4140, Steel 4140PH, steel A36, Steel 4340, etc.
- Stainless steels
- Aluminum alloys
- Cooper
- Titanium
- Brass