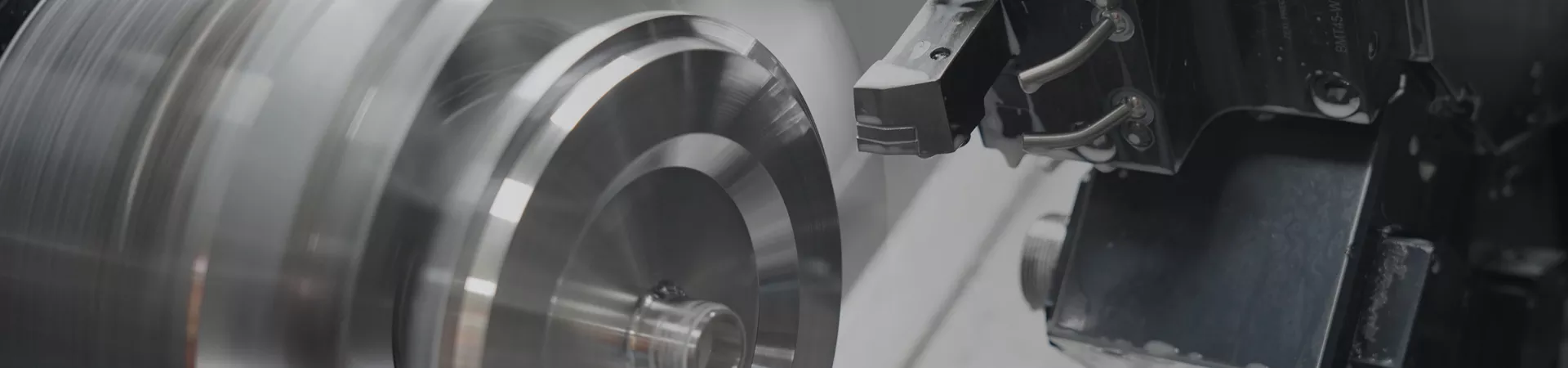
CNC Turning Services
Efficient CNC turning services with fast lead times and competitive pricing from rapid prototyping to production runs. Ensure you get high-quality CNC turned parts with features you need.
GET A QUOTE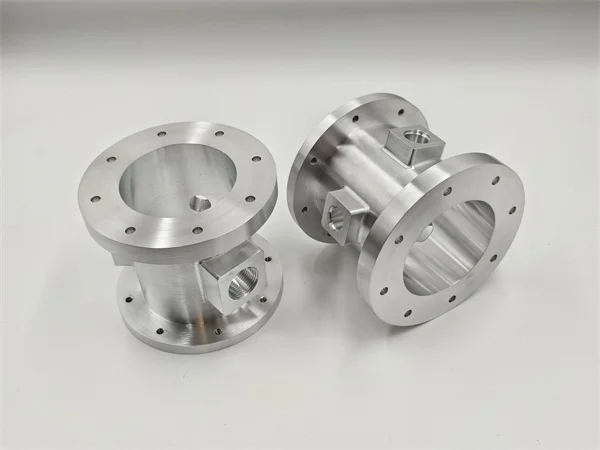
Precision CNC Turning Services for Complex Components
CNC metal turning services provide an effective way to transform a solid chunk of raw metal into a custom finished product designed to your project’s exact specifications. Whether your part requires turning, milling, boring, or tapping, Increase provides enhanced part customization with short lead times. We will work directly with you to provide exceptional service for your CNC Turning requirements.
With advanced technology software and extensive experience working with exotic alloys and specialty metals, Increase has the CNC turning expertise for all your complex machined component needs. We work with CAD and additional software to produce mission-critical components for all types of production volumes.
Our in-house 18” diameter x 20” length Turning centers allow our skilled machinists to form performance-built components from specialty metals. As an industry AS9100 and ISO9001:2015 certified machine shop, we ensure you will receive the high-performance components you want with the mission-critical configurations you need.
Contact a Increase expert or submit an RFQ online and let us machine parts based on your specifications.
From CNC Prototyping to Production
CNC machining is a computerized and versatile manufacturing process ideal for rapid prototyping and on demand production. Here are the custom CNC services available at the Increase.
-
Rapid Prototyping
With our instant quotation platform and strong capacity, you can get excepted prototypes in short lead times. This allows you to quickly test prototype parts and get them to market. -
Bridge Production
Bridge-to-production is critical for closing the gap between the part design and the actual product rollout. No worries. Our professional engineering team is always ready to provide practical design suggestions for your low volume machined parts. -
On-Demand Production
Our full service for on-demand production orders ensures that you get high precison and high standard of quality products. Enhanced production rate also allows for just-in-time delivery of production parts.
Advantages of CNC Turning
CNC lathes remove a lot of material quickly. And when using fine cutting tools such as our Guhring cutters, the surface finish is excellent and doesn’t need any post-finishing. Turning is really the only practical way to make internal and external threads, long bores, tapers, ring grooves, and many other features that are essentially round in cross-section. Some of these same features can also be made on a CNC mill, but this would be slower and is not optimized for maximum efficiency.
Tolerances: Increase can maintain a machining tolerance of +/- 0.003 in. (0.08mm) with a linear tolerance of +/- 0.025 in./in. (0.025mm/mm).