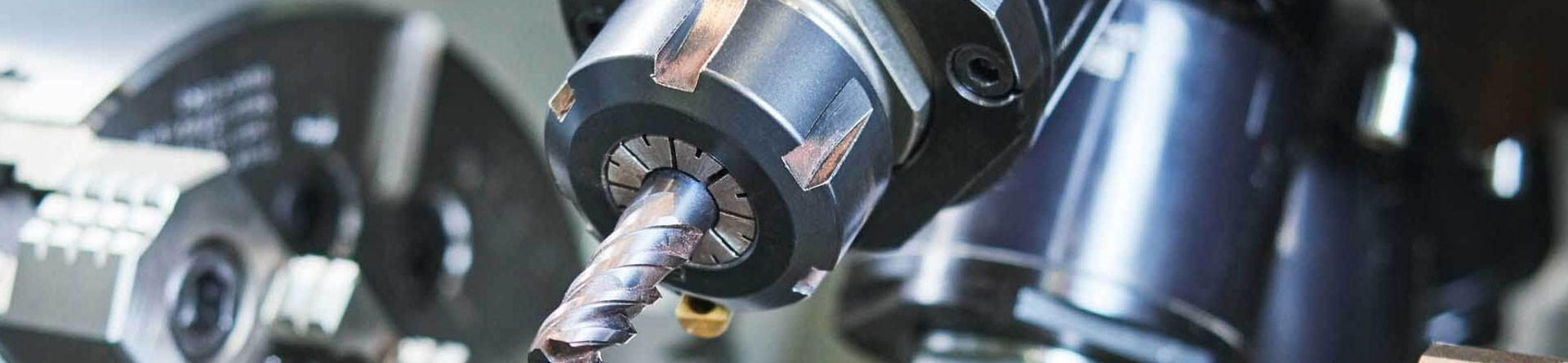
Online Precision CNC Machining Services
Are you in need of a dependable and rapid solution for your machined plastic and metal components? Look no further! Our CNC machining service is here to meet your every requirement. With our unmatched in-house capacity, we guarantee that your parts will be manufactured and shipped promptly, without fail.
Custom CNC machined parts Get An Instant Quote Now!
Our CNC Machining Services
CNC machine all types of parts, from simple “as machined” workholdings to complex geometries. Our manufacturers operate almost every kind of CNC mill and turning center, with EDM and grinders available on request. We offer tolerances down to 0.05 mm (0.0020 in) and lead times from 5 business days.
CNC Machining Tolerances
Achieving precise tolerances in CNC machining is paramount. For metal components, we adhere to ISO 2768 standards, ensuring a general tolerance of up to +/-0.005" or +/- 0.127 mm. However, when it comes to plastics, it's typical to double that tolerance. It's important to note that specific tolerances and size limitations can vary based on factors such as material type, machining technique, and the details provided in your engineering drawings. To ensure the utmost precision for your project, please refer to the following table as a reference, but always consult with our experts for the final determination based on your unique requirements:
CNC Machining Materials
Our CNC services encompass a diverse range of materials, including metals, plastics, and various other material types.
-
Plastic CNC Machining Materials
POM (Delrin), ABS, HDPE, Nylon, PLA, PC, PEEK, PMMA (Acrylic), PP, PTFE, etc. -
Metal CNC Machining Materials
Aluminum, Steel, Stainless Steel, Brass, Copper, Titanium, etc. -
Composite CNC Machining Materials
Carbon fiber, PC glass, PA glass, etc.
CNC Machining Finishes
You can choose a wide selection of metal surface finishing services after machining at Junying CNC machining manufacturer to improve the appearance, surface smoothness, corrosion resistance and other performance of your CNC machined parts. Two surface finishes can be applied on the same part.
Finishing | Description | Materials |
---|---|---|
Standard/As machined | Machines and deburrs parts, chamfers edges | All available metals |
Bead Blast | Reduce machining marks | Aluminum, Titanium, Stainless Steel, Brass |
Anodizing Type II | Creates a thin, porous, corrosion-resistant coating | Aluminum |
Anodizing Type III (Hard coat anodizing) | Creates a hard, thick, wear-resistant porous oxide | Aluminum |
Passivation | Improves corrosion resistance | Steel, Stainless Steel |
Powder coat | Creates strong wear and corrosion-resistant coating | Aluminum, Steel, Stainless Steel |
Tumbling | Removes sharp edges, burrs, and marks | Aluminum, Steel, Stainless Steel, Brass, Copper |
Electropolishing | Improves brightness and reduces corrosion | Steel, Stainless Steel |
Nickel Plating | Creates a nickel coating to resist corrosion, oxidation and wear | Aluminum, Steel, Stainless Steel |
Zinc Plating | Creates a zinc coating to resist corrosion, oxidation and wear | Steel, Stainless Steel |
Black Oxide | Minimizes light reflection and improves corrosion resistance | Steel |
CNC Machining FAQs
What is CNC Machining?
CNC (Computer Numerical Control) Machining is a subtractive manufacturing method, which adopts computerized devices to remove the extra materials from the blank and complete required tasks with CNC machine tools, to produce the final designed CNC machining parts. The machine tool, blade material, speed and feed, blade angle, cutting parameters, coolant, workpiece material, and more factors will affect the quality of the CNC machining service.
How does CNC Machining work?
The CNC machining process generates the final part through the subtraction of material. CNC machines are run by digital computers that control the movement of the equipment. The process of CNC machining will go through:
- Load the CAD (Computer Aided Design) file into CAM (Computer Aided Manufacturing) software.
- Determine tool paths based on the part geometry.
- CAM software creates digital instructions or G-Code tells the machine what to do and how to do it.
- CNC machines execute the operations as the programming language.
What’s the difference between CNC machining and conventional machining?
- Cost. Conventional machining is often less expensive, more cost-effective, and more efficient for smaller jobs. CNC machining is more expensive for little work, but it is more efficient and cost-effective for larger jobs.
- Production. The final conventionally machined product's quality is mostly determined by the machine technician's or operator's skills and talents. Geometry is encoded into the software in CNC machining, reducing the risk of human error in the quality equation.
- Repeatability. Because it is impossible to guarantee a high level of part consistency due to the human factor, traditional machining is best suited for short production runs or a single unit. Because machines are controlled by computer commands, it is simple to create similar parts or components, making CNC machining ideal for the mass production of exceedingly consistent things.
- Requirements. Each machine requires a separate operator, and directing the tools necessitates a large degree of specialist involvement. To make a variety of items, operators of conventional machining must have extensive knowledge, talents, and experience. Because the CNC process requires minimal operator involvement, a single operator may run numerous machines with a high degree of accuracy and precision, lowering labor costs.
What industries use CNC machining or CNC parts?
CNC machining offers parts, components, and products for almost all industries, typical applications are including automotive, aerospace, electronics, agriculture, food, medical, oil and gas, military, marine, household goods, semiconductor, consumer, etc.
Why use CNC machining?
CNC machining is a profitable manufacturing method for precision components, it brings plenty of advantages.
- Minimize the material waste
- Avoid human errors and defects
- Higher accuracy and more efficient production
- Mitigate the possibility of accidents
- Bring down the manufacturing cost
- Decreases the energy losses
What are the standard tolerances of CNC machining?
± 0.005"or 0.13mm is the standard tolerance for machined metal parts,and+/-0.010" is common for plastic parts. The specific tolerance is depending on the material and drawing. We can discuss tight tolerances based on your drawing.